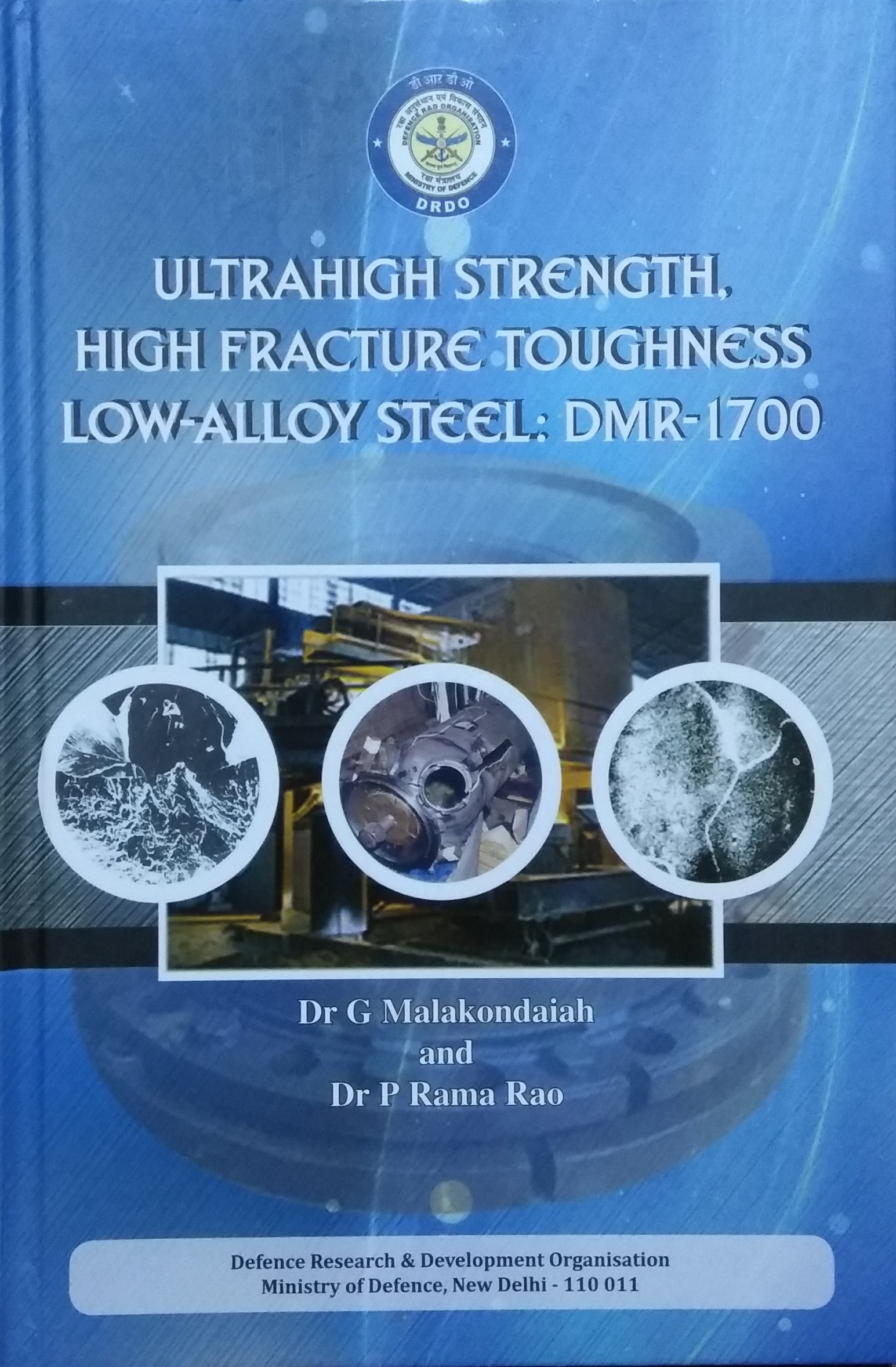
Ultrahigh Strength, High Fracture Toughness Low-Alloy Steel: DMR-1700
$93
Author: | Dr G Malakondaiah and Dr P Rama Rao |
ISBN 13: | 9788186514665 |
Binding: | Hardbound |
Language: | English |
Year: | 2019 |
Subject: | Military Studies |
About the Book
Steels for several high-technology applications, such as military hardware and aerospace, need to possess ultrahigh strength (UHS; minimum yield strength of 1380 MPa (200 ksi)) coupled with high fracture toughness in order to meet the requirement of minimum weight while ensuring high reliability. Broadly, there are four classes of UHS steels: (a) low-alloy steels typified by AISI 4340, (b) high-alloy maraging steels typified by 18Ni1700 steel, (c) high-alloy secondary hardening steels typified by AF1410, and (d) carbide-free bainitic steels. Distinctive characteristics of the UHS low-alloy, maraging, secondary hardening and bainitic steels have been presented in the monograph. In such applications, though performance of materials is of prime consideration, cost and availability make low-alloy steels an attractive option. However, the use of low-alloy steels has often been limited by their low fracture toughness.
A comprehensive research programme was launched at the Defence Metallurgical Research Laboratory (DMRL) during mid-1980s to develop a cost effective low-alloy alternative to the highly alloyed 18Ni1700 maraging steel. The monograph describes the more than three decades of R&D work that led to the research-based development of a new UHS low-alloy steel, designated DMR-1700, its production and its defence applications. The strength and toughness combination of DMR-1700 steel is better than the best reported values of low-alloy steels AISI 4340, 300M and D6ac, and is comparable to that of 18Ni1700 maraging steel. Given this result, DMR-1700 steel has been successfully demonstrated for (a) one-to-one replacement of maraging steel for missile casings, (b) substantial reduction of weight of the base plate for 120 mm long range mortar and (c) superior ballistic performance for armour applications. To address cost effectiveness of DMR-1700, DMRL pursued ladle refining and vacuum degassing + continuous casting route and found that the steel met the chemistry and properties successfully.